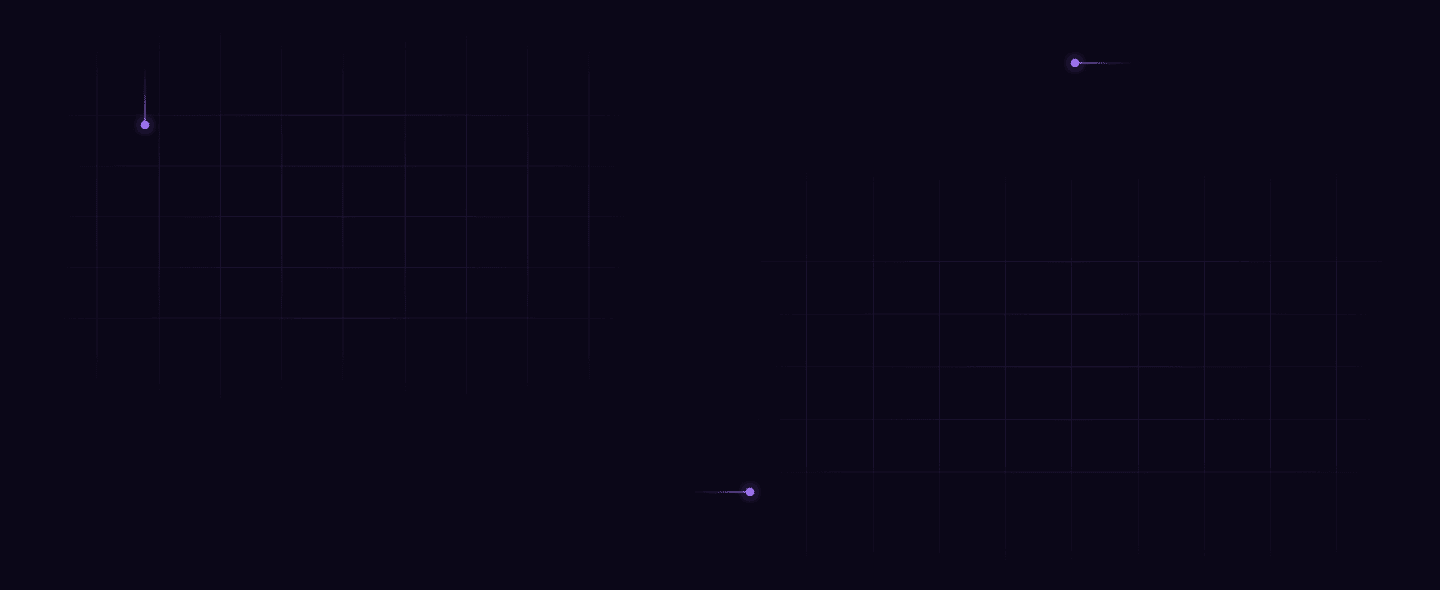
When a single missed defect can trigger a recall, a lost customer, or a reputation you can’t repair, quality control becomes more than just another checkpoint; it’s survival.
The problem is that traditional methods are slow, inconsistent, and collapsing under today’s production speeds and volumes. In fact, manufacturers using AI-driven quality testing see up to a 90% increase in defect detection and 25% lower inspection costs.
If you’re struggling with late defect catches, rising rework costs, or customer complaints, AI is the fastest, smartest way to detect issues early, prevent costly failures, and finally build a production line you can trust at scale.
This post breaks down exactly how AI transforms quality control and the steps to overcome challenges with implementing AI for quality control.
The role of AI in quality control
AI is transforming quality control in manufacturing by shifting from reactive inspections to proactive defect prevention. Traditional methods often rely on human observation, which can miss subtle issues and slow down production. AI enhances this process by using computer vision and machine learning to detect defects earlier and more accurately.
AI vs traditional quality control
Traditional quality control often relies on manual inspections and judgments, which can be inconsistent and subjective. This method may be more accessible initially due to lower setup costs, but it lacks the speed and data-driven precision that AI provides. Moreover, traditional methods struggle to scale efficiently as production volumes increase, making them less suitable for modern, high-demand manufacturing environments.
6 Benefits of using AI in quality control
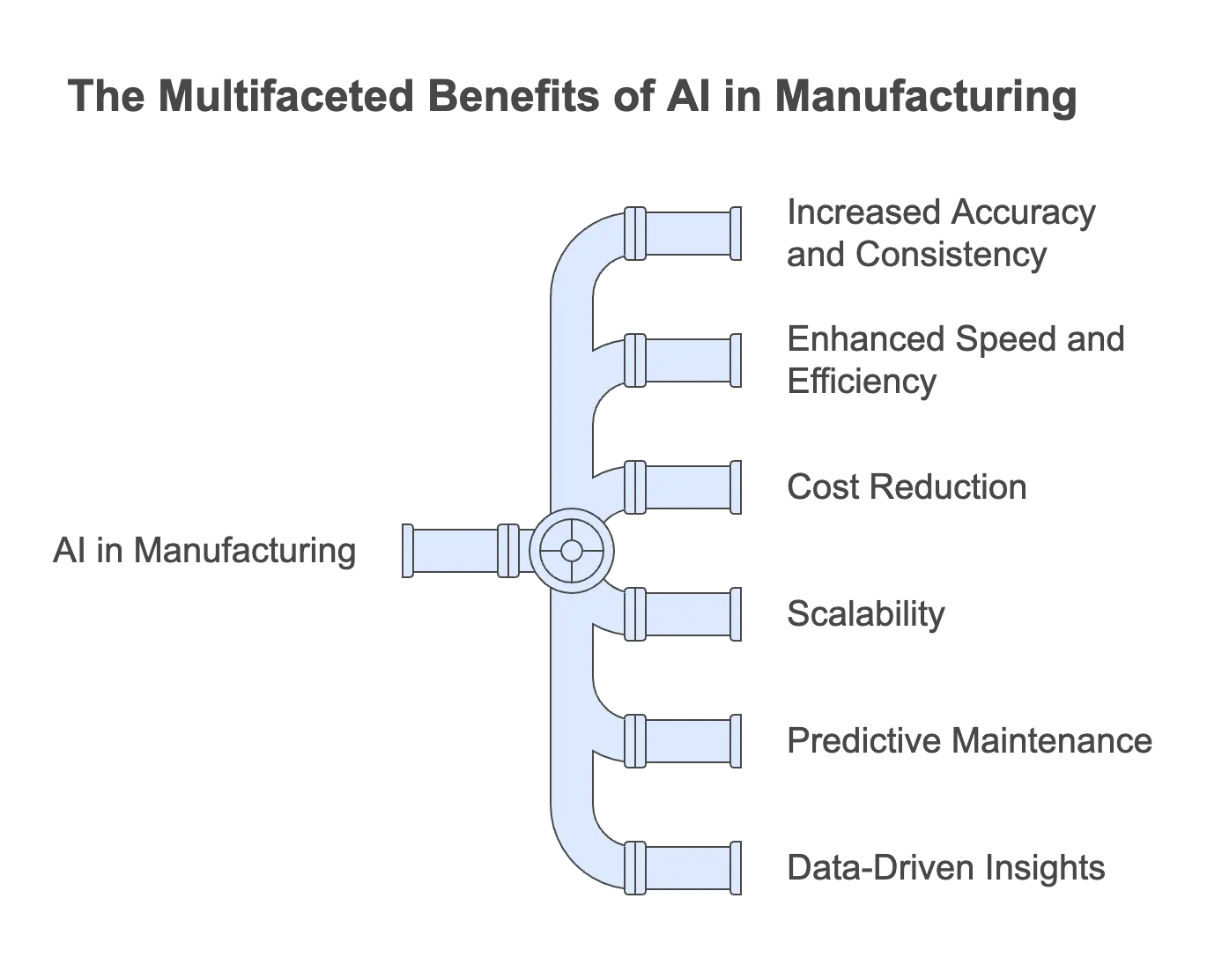
The use of AI in quality control manufacturing brings numerous benefits that directly contribute to the efficiency, reliability, and profitability of manufacturing processes. Here are some key advantages, accompanied by real-world examples:
#1 Increased accuracy and consistency
AI-driven systems analyze data with a level of precision that far surpasses human capabilities, leading to fewer defects and a higher quality end product. For example, Intel uses AI to inspect microprocessor fabrication, identifying defects in silicon wafers with far greater accuracy than traditional methods. This precision helps prevent costly recalls and maintains the brand's reputation for quality.
GM has partnered with Nvidia to utilize AI chips and software for automating vehicle manufacturing processes. This collaboration aims to improve factory workflows and enhance quality control by integrating AI into production lines.
#2 Enhanced speed and efficiency
AI systems process and analyze data at speeds unattainable by human workers. This rapid analysis allows for real-time quality control, which significantly speeds up the production process. Nissan Motor Corporation utilizes AI to streamline paint defect detection on its assembly line, reducing inspection time by about 75% and significantly accelerating overall production flow.
Pfizer has integrated AI into its clinical trials to perform quality-checks and analyze lots of patient data at 50% faster speed. Building on this success, AI and ML capability are used in more than half of all Pfizer’s clinical trials.
#3 Cost reduction
While AI requires initial investment, it drastically reduces costs over time by minimizing waste, reducing the need for reworks, and optimizing the use of materials. GE Healthcare reported a 30% reduction in inspection costs by employing AI technologies to detect anomalies in medical equipment manufacturing, showcasing substantial cost savings.
#4 Scalability
AI systems can easily scale to accommodate different production volumes and complexities without significant additional costs. This scalability is evident in companies like Tesla, where AI-driven robots and quality control systems allow for rapid scaling of production lines for new models, adapting quickly to market demands.
BMW has integrated advanced AI technologies into its manufacturing operations to improve quality assurance and production efficiency. One notable implementation is the AIQX (Artificial Intelligence Quality Next) platform, which utilizes sensor technology and AI to automate quality processes. By establishing camera systems and sensors along the conveyor belt, AIQX analyzes data in real-time and provides immediate feedback to production line employees via smart devices. This system helps determine variants, check completeness, and detect anomalies in the assembly process.
#5 Predictive maintenance
AI not only detects defects but can also predict potential machine failures before they occur, ensuring uninterrupted production. Siemens has deployed AI-based systems that monitor equipment and predict maintenance needs, reducing downtime and improving overall plant efficiency.
#6 Data-driven insights
AI systems provide valuable insights that can lead to continuous improvement in production processes. Bosch, for instance, uses AI to analyze production data across its manufacturing sites, identifying patterns that lead to defects and enabling proactive adjustments to improve quality.
6 Steps to overcome challenges with AI in quality control
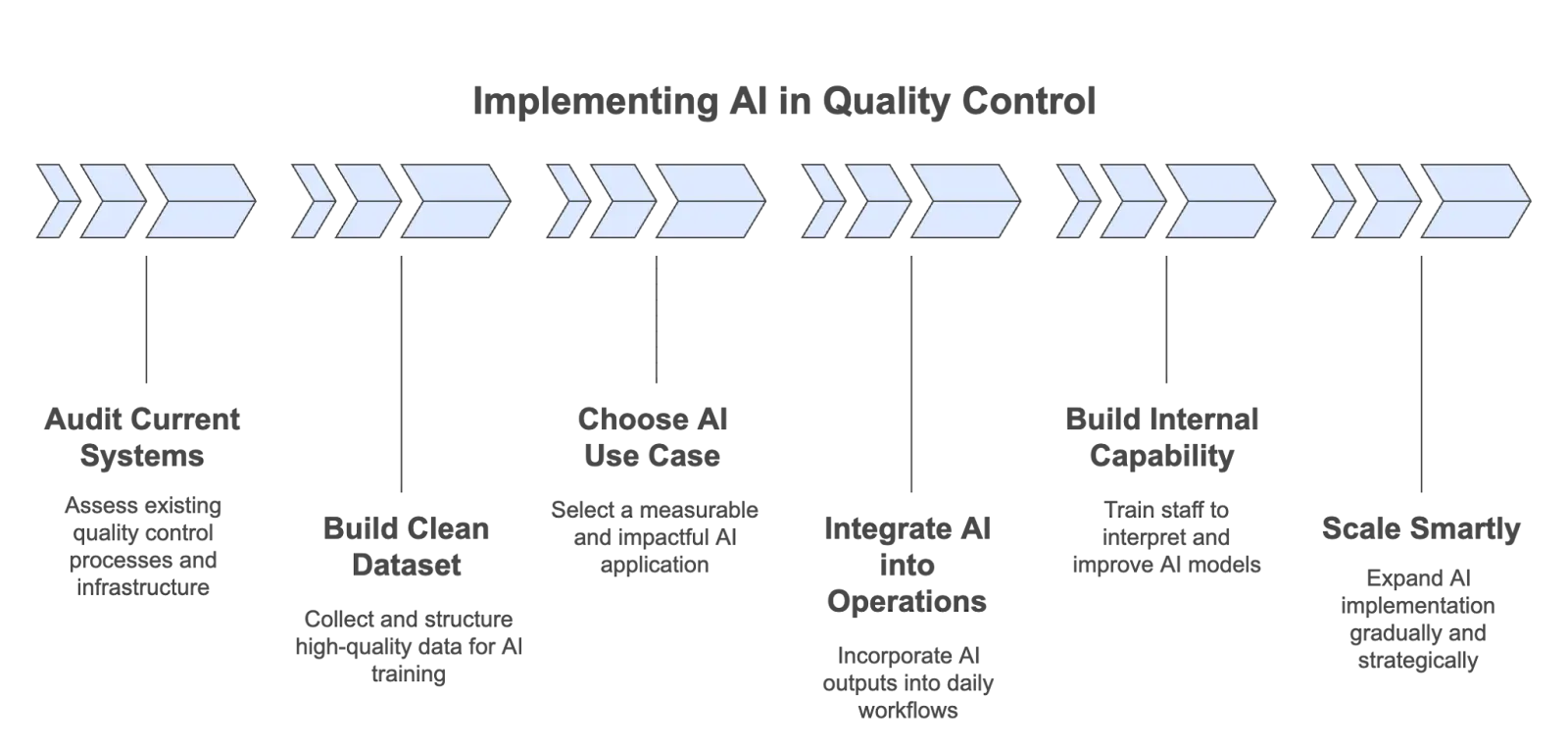
AI can dramatically improve defect detection and quality control. But rolling it out isn’t plug-and-play—you need a smart, structured approach. Here's how to get started:
Step 1: Audit your current systems and processes
- Map where quality control happens today—manual checks, machine inspections, random sampling
- Identify gaps: where defects slip through, where inspection is slow, where human error is likely
- Assess your IT and data infrastructure: are critical quality control systems connected digitally or still siloed
Tip: Focus first on one production line or process with high defect rates and clear business impact.
Step 2: Build a clean, usable dataset
AI is only as good as the data you feed it. If your data is scattered, incomplete, or dirty, even the best AI models will fail. Building a structured, high-quality dataset is non-negotiable.
“Better AI isn't just about more data. It is about the quality and the connected data. This is a complex challenge for several reasons, apart from data quality.”
~ Anindita Misra, VP of Data, Decathlon
How Decathlon uses data to optimize in-store operations
Here’s how to start:
- Collect data from your machines, sensors, cameras, ERP, MES, and manual QC systems
- Focus on structured, timestamped records: production parameters, inspection logs, visual inspection images, machine usage patterns
- Set up simple pipelines at first—CSV exports, cloud folders, basic APIs—to centralize data into one place
- Ensure you have at least a few months of historical data to spot patterns and train early AI models
Getting your data together sounds simple but is often the hardest part.
And this is where 5X comes in. We connect to your existing systems—ERP, CRM, spreadsheets—and build a unified, organized data foundation.
With 5X, you don’t need to spend months building custom ETL pipelines or cleaning up messy system outputs. You get a real-time, business-ready data environment that feeds directly into quality control AI models—and scales easily when you're ready to expand to predictive maintenance, production optimization, or supply chain insights.
Step 3: Choose your first AI use case wisely
- Pick a use case that is easy to measure and offers quick wins—for example, surface defect detection, part misalignment, or missing component identification
- Start with narrow AI models like machine vision or simple anomaly detection before scaling to complex predictive models
Step 4: Integrate AI into daily operations, not as a side tool
- Connect AI outputs directly into operator dashboards, production alerts, or maintenance systems
- Make sure production staff can act on AI signals immediately—no long handoffs, no bottlenecks
- Track real outcomes: reduced rework, faster defect detection, higher yield
“Data transformation is about the culture. We are empowering our teams to work with data in new ways while making sure we don't fall back into the data silos again. That requires considerable data literacy effort. Describing data is really becoming more and more important, especially when we talk about innovation at scale with AI.”
~ Anindita Misra, VP of Data, Decathlon
How Decathlon uses data to optimize in-store operations
Tip: The more naturally AI fits into daily work, the faster adoption happens.
Step 5: Build internal capability step-by-step
- Train your engineers, line managers, and quality teams on how AI models work—not to code, but to interpret and improve them
- Set up small cross-functional squads (manufacturing + IT + quality) to run early pilots
- Share wins internally to build momentum for larger deployments
Step 6: Scale smart, not fast
- Once the first project delivers results, replicate it to adjacent production lines or processes
- Keep refining: retrain models regularly with new data, tweak thresholds, improve feedback loops
- Expand carefully: prioritize scaling where the business case is strongest
Tip: Phased implementation controls cost and risk better than trying to transform everything at once.
AI-powered quality control isn’t optional anymore
AI is rewriting the rules of modern manufacturing. What started as an experiment in defect detection has become a critical lever for operational excellence, product reliability, and market leadership.
We’ve seen how AI shifts manufacturing from reactive inspections to real-time, predictive quality assurance. Companies using AI aren’t just catching defects faster; they’re scaling smarter, slashing costs, and building products that consistently meet rising customer expectations. Sure, challenges like system integration and upfront costs exist. But the payoff (higher yield, reduced waste, faster time-to-market) is making AI a non-negotiable for any manufacturer serious about competing in the future.
The good news? You don't have to figure it all out alone.
At 5X, we help you unlock the full power of your data without tearing apart your existing systems. We organize your production, quality, and operations data into a unified foundation, model it intelligently, and help you build AI applications that catch defects before they happen—all on your infrastructure, at your pace.
FAQs
How can manufacturing quality be controlled with AI?
Building a data platform doesn’t have to be hectic. Spending over four months and 20% dev time just to set up your data platform is ridiculous. Make 5X your data partner with faster setups, lower upfront costs, and 0% dev time. Let your data engineering team focus on actioning insights, not building infrastructure ;)
Book a free consultationHere are some next steps you can take:
- Want to see it in action? Request a free demo.
- Want more guidance on using Preset via 5X? Explore our Help Docs.
- Ready to consolidate your data pipeline? Chat with us now.
Table of Contents
Get notified when a new article is released
Get an end-to-end use case built in 48 hours
Get an end-to-end use case built in 48 hours
How retail leaders unlock hidden profits and 10% margins
Retailers are sitting on untapped profit opportunities—through pricing, inventory, and procurement. Find out how to uncover these hidden gains in our free webinar.
Save your spot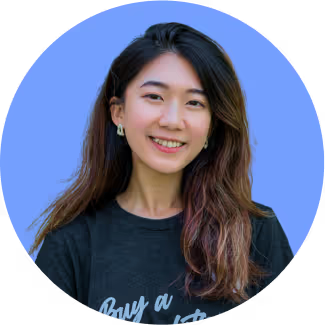
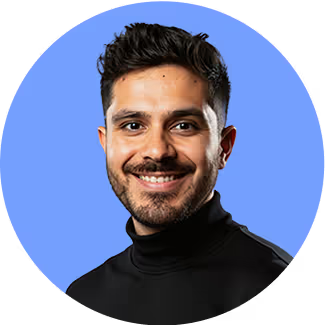