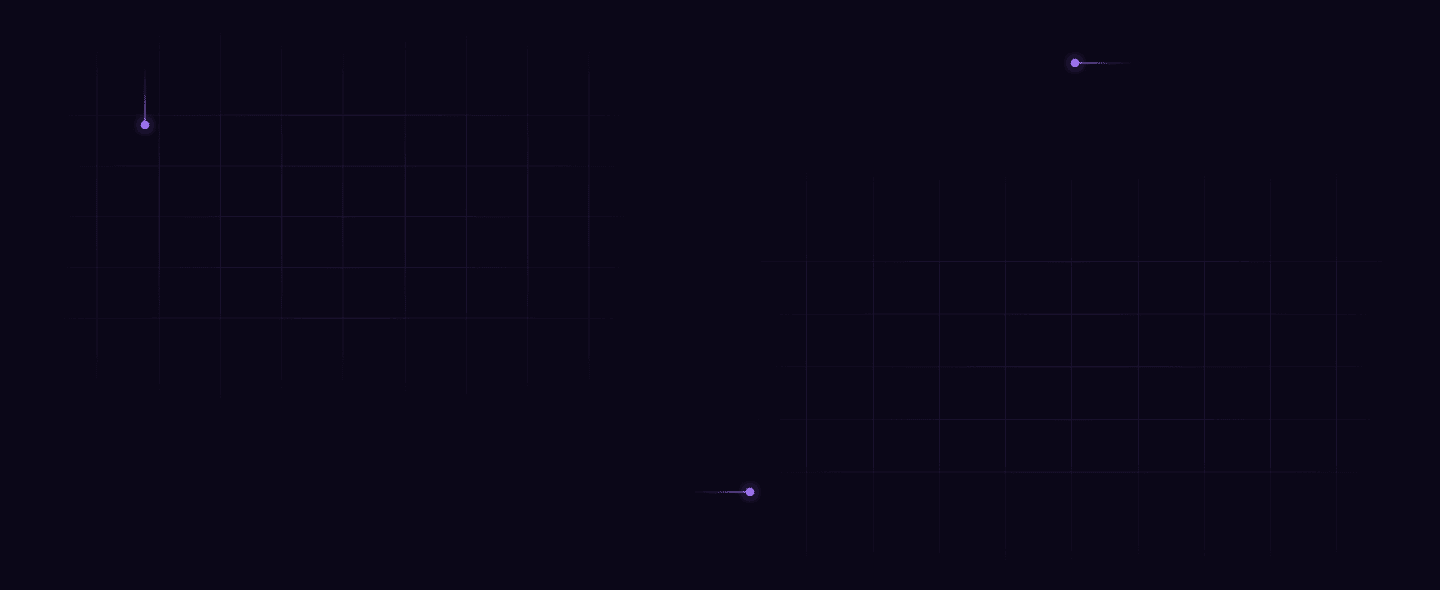
First, there were hands. Then came hammers. Then came machines. And now, there’s AI, transforming quality assurance in production lines like never before!
AI is building effective production lines by enforcing smarter and more intuitive quality checks. Using AI, factories don’t just produce — they learn, adapt, and improve, cycle after cycle.
Read this blog to understand how you can improve quality in production lines using AI.
Understanding the role of AI in production line QA
Traditionally, factories relied on paper checklists, human eyes, and hours of observation to track performance and spot problems. It worked. But it wasn’t enough. Errors slipped through, time was wasted, and people were overworked. Now, everything is changing with AI.
AI doesn’t blink or get tired. The beauty of AI is it doesn’t miss a thing. AI watches every product, at every stage. It checks for flaws in real time and flags defects before they become disasters. It uses computer vision to spot the tiniest misalignment. It also uses machine learning to know what “just right” really looks like. And it does this over and over, all day long.
For manufacturers, this translates to fewer errors, faster output, less waste, more consistency, and more confidence that comes from a job well done.
QA challenges of using traditional methods in production lines
For decades, quality assurance in manufacturing has largely depended on manual inspection and human oversight. While this approach has been effective to some extent, it also presents many challenges. Here are some key quality assurance (QA) challenges manufacturers face when using traditional methods on the production line:
- Inconsistency: One of the most pressing issues with traditional QA methods is the risk of human error. Inspectors may miss subtle defects due to fatigue, oversight, or inconsistent interpretation of quality standards. This variability often results in inconsistent outputs, where one batch may meet the required standards while another does not, even though both have passed inspection
- Time-consuming: Time is another major factor. Manual inspection is inherently slow, particularly in high-volume environments where every component or product needs to be checked. As a result, production lines can get delayed, and any error caught late in the process may require significant rework or lead to costly scrap
- Missed defect detection: Traditional QA is more reactive than proactive. Defects are often identified after they occur, not prior. This increases operational costs and risks defective products reaching the market, which can damage brand reputation
- Scale and efficiency: As production scales up, so do the limitations. Training more human inspectors, ensuring consistent evaluations, and maintaining detailed documentation becomes harder and more expensive, ultimately affecting both scalability and efficiency
These challenges clarify that traditional QA alone can no longer keep up. It’s time for manufacturers to explore smarter, more scalable alternatives.
How does AI improve quality assurance in production lines?
AI brings precision, speed, and consistency to quality checks, helping manufacturers catch errors early, reduce costs, and boost overall productivity. Here’s how:
- Ensures process compliance: AI-powered computer vision systems can verify that each step in the assembly process follows standard operating procedures (SOPs). In automotive lines, it can confirm that bolts are tightened in the right order or parts are placed correctly
- Instant Error Detection: On manual lines, AI catches issues like missing parts, incorrect placements, or faulty techniques. It alerts operators or supervisors immediately, helping prevent defects from moving further down the line
- Kitting validation: In industries like electronics or aerospace, AI systems ensure that the right components are included in kits before assembly begins, minimizing errors and avoiding delays caused by missing or incorrect parts
- Real-time operator feedback: AI empowers manufacturers to address issues at the source, leading to higher yields and reduced scrap rates. It achieves this by providing live guidance to operators, allowing them to fix mistakes on the spot. This boosts output quality, shortens training time for new workers, and improves overall efficiency
- Accurate defect detection: AI-powered systems can detect even the slightest deviations from established specifications, ensuring that all products meet the required quality standards
- Lower costs, higher throughput: With AI, fewer human inspectors are needed. Plus, it inspects much faster—cutting costs and speeding up time-to-market
- Smarter decisions with real-time data: AI analyzes production data in real time, giving manufacturers actionable insights to optimize processes and fix issues quickly.
- Predicts and prevents defects: By spotting patterns in production data, AI can forecast potential quality problems, allowing preventive action before issues arise
Benefits of using AI in production lines for operators and engineers
A factory runs on machines, but it thrives on people. On the floor, operators build, assemble, move, and execute. Engineers fine-tune the process and look for a better way to improve processes.
Together, they are the heartbeat of production. Here’s how AI benefits both.
How AI benefits operators:
On the production floor, operators are at the heart of every assembly task. But complex procedures, tight timelines, and high expectations can make manual work stressful and error-prone.
AI tools are changing that. Here’s how:
- Step-by-step guidance: AI tools offer real-time, step-by-step instructions during complex assembly tasks. This reduces the need for advanced training and helps operators complete their work accurately and confidently
- Instant error detection and correction: Using machine learning and computer vision, AI instantly flags errors such as missed steps or incorrect actions, allowing operators to fix them immediately. This reduces the chances of mistakes going unnoticed
- Less cognitive strain, more confidence: Real-time support reduces the mental burden on operators. They don’t have to memorize every step anymore. This results in lower stress level and improved consistency
- Improved safety and efficiency: Visual intelligence tools can spot unsafe practices and help optimize how operators interact with tools, machines, and materials, leading to safer and more efficient workflows
How AI benefits engineers:
For engineers, improving line performance and reducing inefficiencies has always involved hours of observation, data collection, and guesswork. With AI, that manual effort is replaced by instant, video-based insights. Engineers can now detect problems faster, analyze patterns at scale.
Here’s a breakdown:
- Faster diagnostics and root cause analysis: AI can analyze a single workstation video and offer instant insights, eliminating the need for manual data collection, time-consuming note-taking, or walking the floor with a stopwatch
- Real-time productivity monitoring: Engineers can use AI to track every step of the assembly process across shifts, lines, and locations. This helps them identify bottlenecks, inefficiencies, and best practices with ease
- Scalable time-motion studies: Instead of traditional manual studies, engineers can now run hundreds of time-motion analyses per week using AI. This brings scale, speed, and accuracy to process optimization
- Actionable process improvement insights: Ai analyze operator movements and task allocation to suggest layout changes, better line balancing, or ergonomic improvements, saving time and reducing waste
- Enhanced traceability: AI maintains a complete video log of each assembly cycle. This makes it easier to trace defects back to their source, whether they come from operator error, machine failure, or process issues
- Better quality and first-pass yield: With real-time monitoring and feedback, errors are prevented. This leads to higher-quality output, less rework, and fewer recalls
The 5X advantage: How 5X powers quality assurance
Implementing AI for quality assurance is only as effective as the data that powers it.
That’s where 5X steps in. 5X offers manufacturers a seamless way to bring together scattered data sources and turn them into actionable insights.
5X integrates quality inspection data, test results, process parameters, and production records from existing systems to create a unified business intelligence view. This view eliminates data silos and allows teams to track product performance and process consistency in real time.
But 5X doesn’t stop there. It digs into your historical data, connects the dots, and finds patterns. It shows how one tiny change in a process might be creating a big dip in quality. And the best part is that you don’t need expensive new sensors. Just the data you already have.
With 5X, you go from reacting to problems to predicting them. You cut down rework. You prevent waste. You build better products, faster. That’s smart quality assurance.
Conclusion
AI is enhancing quality assurance and transforming it into a strategic advantage. By automating inspections, predicting defects, and providing real-time feedback, AI empowers both operators and engineers to deliver higher quality at scale, with less rework and downtime.
As factories evolve into smart manufacturing ecosystems, AI-led QA ensures that excellence is built into every step of the process. For forward-thinking manufacturers, the question isn’t if they should adopt AI in QA, it’s about how soon they can get started.
FAQs
How can AI be used in quality assurance?
How to use AI in QA testing?
What is production quality assurance?
Building a data platform doesn’t have to be hectic. Spending over four months and 20% dev time just to set up your data platform is ridiculous. Make 5X your data partner with faster setups, lower upfront costs, and 0% dev time. Let your data engineering team focus on actioning insights, not building infrastructure ;)
Book a free consultationHere are some next steps you can take:
- Want to see it in action? Request a free demo.
- Want more guidance on using Preset via 5X? Explore our Help Docs.
- Ready to consolidate your data pipeline? Chat with us now.
Table of Contents
Get notified when a new article is released
Get an end-to-end use case built in 48 hours
Get an end-to-end use case built in 48 hours
How retail leaders unlock hidden profits and 10% margins
Retailers are sitting on untapped profit opportunities—through pricing, inventory, and procurement. Find out how to uncover these hidden gains in our free webinar.
Save your spot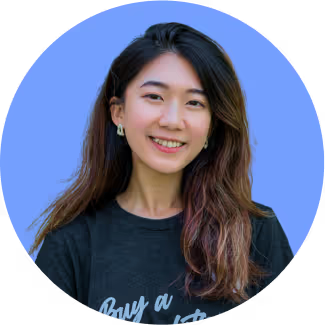
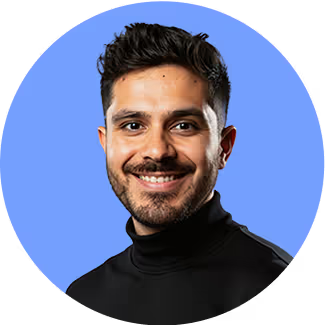