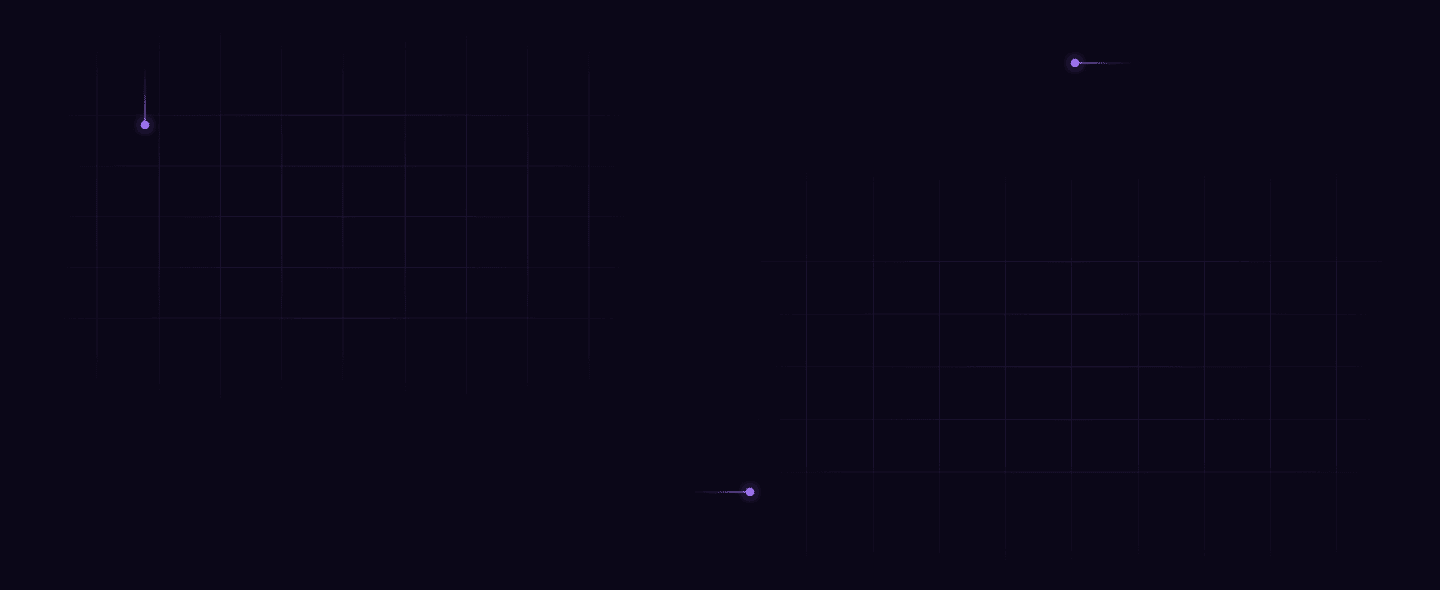
Manufacturing is a game of margins. Every machine breakdown, every defective part, every delay eats into profitability. The problem isn’t that manufacturers don’t know this – it’s that they often don’t have the visibility or tools to fix it before the cost piles up. AI changes that.
AI does not replace people but gives them quick and efficient visibility into patterns they could never spot on their own. And when manufacturers start using AI to see what’s actually driving their costs, they can stop wasting money in ways they never even realized.
Read this blog to understand AI’s role in manufacturing, how it reduces costs, its benefits, and some frequently asked questions that will help you understand if AI adoption is right for you.
The role of AI in manufacturing:
AI is reshaping manufacturing, not as a distant promise but as a present reality. It processes vast amounts of data at speeds impossible for humans, uncovering inefficiencies, predicting outcomes, and automating tasks that once required manual effort.
As a result, AI empowers manufacturers to uncover hidden insights, make data-driven decisions, and automate repetitive tasks. It plays a transformative role in manufacturing by optimizing efficiency, improving quality, reducing costs, and enhancing decision-making.
How AI reduces manufacturing costs:
Manufacturing is a balancing act. Everything comes with an attached cost. Reduce waste, and profits rise. Cut inefficiencies, and production accelerates. Here’s how AI reduces manufacturing costs:
1. Reduce quality-related costs (Rework, scrap, recalls)
A small flaw in a part. A slight misalignment. Maybe a process that works fine in one shift but produces defects in another. On paper, these seem minor. But if those defective parts move down the line, they can end up assembled, shipped, and even installed in vehicles before anyone notices.
The cost? Rework. Scrap. Sometimes even a full-blown recall.
AI changes this by connecting every piece of quality data such as inspection reports, production logs, and even past defect patterns. It doesn’t just tell you when something is wrong. It tells you why.
AI shows that maybe defects spike when a specific machine runs at high speed. Or that parts made from a certain supplier’s batch fail more often. This isn’t just about catching bad parts but preventing them from happening in the first place which means fewer defects, less scrap, and lower costs.
5X data platform intervention:
5X connects quality inspection data, test results, process parameters, and production records into a single quality business intelligence system. Its AI analyzes historical patterns to find links between production variables and quality outcomes without requiring extra sensors.
2. Optimize equipment effectiveness (Reduce downtime and improve OEE)
When a machine fails, production stops. Operators reset it. Maintenance teams scramble. The plant loses money with every passing minute.
What’s frustrating is that most breakdowns aren’t random. Machines give subtle warning signs before they fail such as slight temperature increases, tiny shifts in vibration, and unusual cycle times.
Humans can’t track these patterns across thousands of machines. AI can.
By analyzing historical maintenance data, equipment logs, and real-time signals, AI can predict failures before they happen. AI will share updates in the following ways:
- This press is showing early signs of wear → schedule maintenance next week before it fails
- This conveyor has a 90% chance of breaking down in 300 hours → plan for it now
This results in fewer unexpected shutdowns. Lower maintenance costs. Less wasted time. And a production line that keeps running smoothly.
5X data platform intervention:
5X combines data from MES systems, downtime logs, quality records, and shift reports to create clear OEE dashboards with actionable insights. Our AI Analytics models analyzes past data to spot downtime patterns and efficiency losses, helping manufacturers improve operations
3. Reduce energy consumption (Lower utility bills)
Manufacturers use a lot of energy. But they don’t often know where they’re wasting it. For example, machines run at full power when they don’t need to. HVAC systems overcool empty areas. Compressors cycle inefficiently.
AI uncovers this waste by linking energy data to actual production needs. It learns how much power each process really requires and identifies where energy is being wasted.
Then it recommends simple fixes:
- Lower power settings for certain machines during low-demand periods
- Better scheduling to reduce peak energy loads
- Smarter cooling and lighting strategies
These aren’t theoretical ideas. They’re small, practical adjustments that, when applied across an entire plant, lead to massive cost savings.
5X data platform intervention:
5X connects utility bills, production records, shift schedules, and facility data to link energy use with production. Its AI detects waste patterns and finds ways to optimize energy efficiency.
4. Minimize inventory & supply chain costs
In an attempt to not run out of materials, manufacturers tend to stock extra. The problem is that too much inventory ties up working capital. And too little inventory leads to delays, expensive rush orders, and lost production time.
AI helps manufacturers find the right balance. It analyzes supplier lead times, historical demand, and real-time production data to forecast exactly how much inventory is needed. This means:
- Less money locked up in excess stock
- Fewer last-minute emergency purchases
- A supply chain that moves at the right speed without waste
5X data platform intervention:
5X connects supplier data, logistics, inventory, and production needs to give full supply chain visibility. It detects risks and recommends ways to prevent disruptions.
5. Optimize production planning and scheduling
Every shift, manufacturers juggle priorities that include:
- Maximize production
- Minimize machine changeovers
- Reduce overtime
- Deliver on time
But the moment something changes — whether it’s an urgent order, a machine issue, or a delayed shipment, the entire plan falls apart.
AI prevents this chaos by continuously analyzing constraints and recalculating the best way forward. Instead of reacting to disruptions, manufacturers can proactively adjust before problems escalate. This results in less wasted time, lower labor costs, and a more efficient production flow.
5X data platform intervention:
5X uses AI to analyze past production, current orders, material availability, and equipment constraints to create optimal production plans. The AI apps continuously adapt in real time and recommend the best scheduling adjustments as conditions change.
Benefits of using AI in manufacturing
AI integrates data from across the production process to uncover inefficiencies, predict failures before they happen. Here are some benefits enjoyed by manufacturers who embrace AI:
- Quality improvement & root cause analysis: AI integrates and analyzes quality inspection data, test results, and production records to detect patterns that lead to defects. It helps manufacturers identify correlations between production variables and quality outcomes. This enables faster and more accurate root cause analysis without needing direct sensor data
- Equipment effectiveness & downtime reduction: By consolidating production data from various systems (MES, downtime logs, shift reports), AI provides OEE (Overall Equipment Effectiveness) dashboards and identifies patterns of downtime. This allows manufacturers to take proactive steps to improve efficiency
- Predictive maintenance: AI eliminates the inefficiencies of fixed maintenance schedules by analyzing historical maintenance records, equipment usage, and repair histories. It predicts potential failures and suggests data-driven maintenance schedules. This reduces unnecessary maintenance costs and unexpected breakdowns
- Energy efficiency & sustainability: AI correlates energy consumption with production activities by analyzing utility billing data, production schedules, and shift reports. This allows manufacturers to identify energy waste and optimize energy usage without installing additional sensors
- Supply chain resilience & risk management: AI improves end-to-end supply chain visibility by integrating supplier data, logistics information, and inventory levels. It helps predict disruptions and suggests mitigation strategies, reducing the impact of supply chain shocks
- AI-powered production planning & scheduling: AI helps production planners optimize schedules by analyzing historical production data, current orders, material availability, and equipment constraints. It enables dynamic adjustments in real time to balance throughput, efficiency, and delivery timelines
- Smart assembly line balancing: AI detects workstation imbalances and bottlenecks by analyzing production records and time measurements. It then recommends optimal workstation assignments and real-time adjustments to improve the amount of material or items passing through the manufacturing process
- Optimized material flow & inventory management: AI analyzes material movements, production schedules, and shop floor layouts to optimize material delivery and reduce excess inventory to minimize waste and inefficiencies
- Faster new product introduction: AI consolidates historical launch data to create a knowledge base for predictive analytics. This helps manufacturers anticipate and mitigate issues in new product introductions, reducing time-to-market delays
- Tool lifecycle management: AI integrates tool usage records, maintenance history, and production data. As a result, it enables data-driven tool maintenance and replacement decisions, extending tool lifespan and reducing costs
Leading automotive manufacturers choose 5X:
Automotive manufacturing runs on data, but that data is often fragmented, siloed, and underutilized. 5X changes that. Its purpose-built solution is designed to unlock the full potential of your existing systems and pave the way for AI-driven transformation in manufacturing.
- Designed for automotive, built for impact: 5X understands the unique challenges of automotive manufacturing, from quality control to production optimization, without requiring costly new sensor infrastructure
- Works with what you have: Instead of replacing systems, 5X integrates with your ERP, MES, PLM, and quality platforms, extracting untapped value from the data you already collect
- Faster insights, quicker results: With pre-built data models and industry-specific analytics, 5X accelerates time-to-value, eliminating the need for complex customizations
- One platform, limitless possibilities: From data integration to AI-powered insights, 5X provides an all-in-one solution for analytics, visualization, and optimization
- A foundation for the future: As AI and Industry 4.0 continue to reshape manufacturing, 5X ensures you’re ready. It creates a scalable data infrastructure that evolves with your needs, positioning your factory for continuous improvement and innovation
The bottom line: AI turns invisible costs into visible savings
Most manufacturing waste isn’t obvious. It’s hidden in small inefficiencies such as extra scrap, a few extra minutes of downtime, and slightly higher energy use every hour. Over time, these small costs add up.
AI exposes these hidden costs. It finds patterns and delivers specific and actionable insights that let manufacturers cut costs without cutting quality or output.
The manufacturers who use AI will stay ahead. The ones who don’t will lose money without ever realizing where it’s going. Consult 5X to reduce your manufacturing costs using AI today!
How can AI be used to reduce manufacturing costs?
How can AI help the manufacturing industry?
How to reduce costs in manufacturing without AI?
Will AI reduce labor costs?
Building a data platform doesn’t have to be hectic. Spending over four months and 20% dev time just to set up your data platform is ridiculous. Make 5X your data partner with faster setups, lower upfront costs, and 0% dev time. Let your data engineering team focus on actioning insights, not building infrastructure ;)
Book a free consultationHere are some next steps you can take:
- Want to see it in action? Request a free demo.
- Want more guidance on using Preset via 5X? Explore our Help Docs.
- Ready to consolidate your data pipeline? Chat with us now.
Table of Contents
Get notified when a new article is released
Get an end-to-end use case built in 48 hours
Get an end-to-end use case built in 48 hours
How retail leaders unlock hidden profits and 10% margins
Retailers are sitting on untapped profit opportunities—through pricing, inventory, and procurement. Find out how to uncover these hidden gains in our free webinar.
Save your spot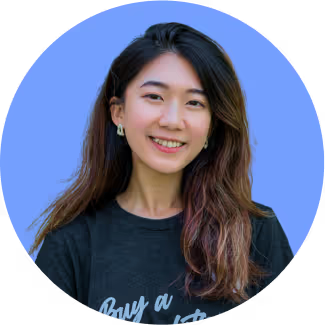
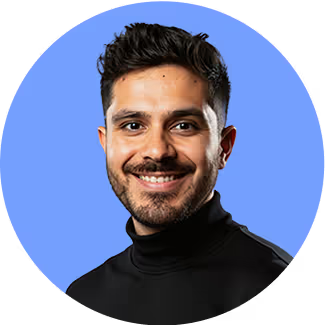