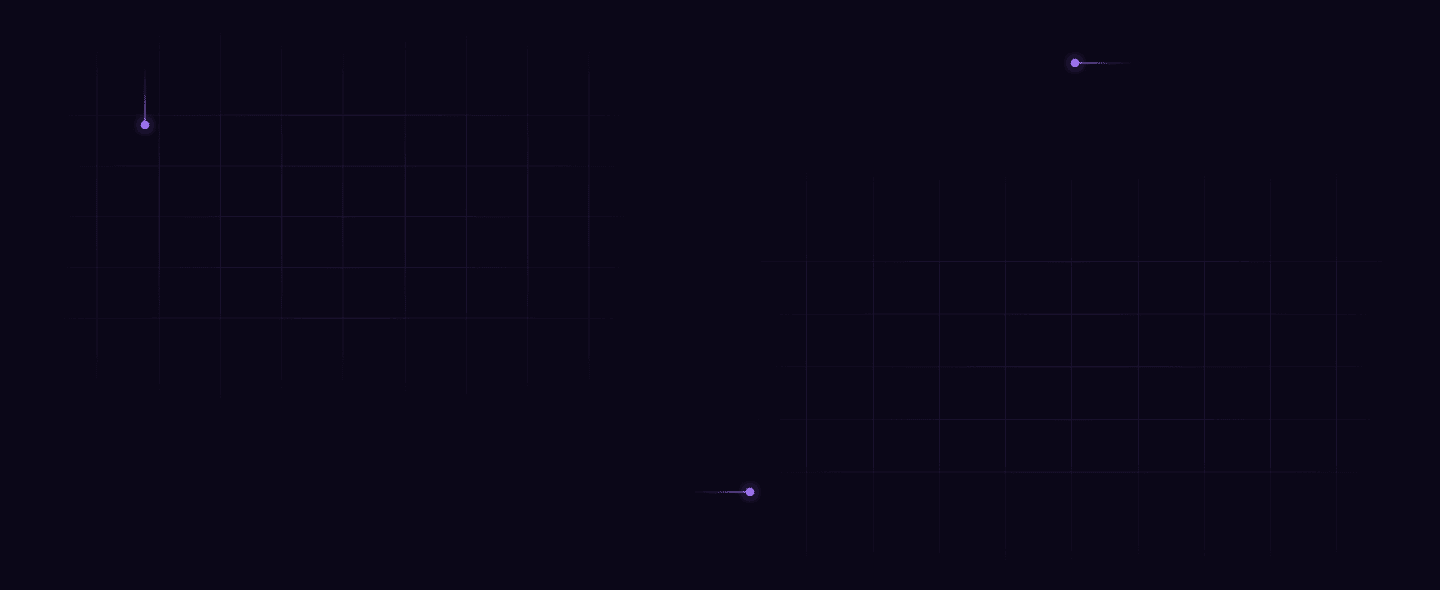
Imagine trying to scale production with systems that can’t keep up. Your machines are running. Your teams are working. But deadlines slip, output plateaus, and every improvement feels like pushing a boulder uphill.
The problem isn’t effort. It’s visibility.
Your data is slow, your tools are reactive, and your processes were designed for a different pace of business. You’ve probably outgrown your current setup, but haven’t had the time (or the clarity) to rethink it.
This is where AI changes the game. You get faster decisions, fewer delays, and predictable, measurable output.
In this post, we’ll show you how to optimize your production line using AI. You will learn how to track what’s really happening, fix what’s dragging you down, and redesign your operations for the speed and flexibility today demands.
What is production line optimization?
Optimizing a production line means making the entire process, from raw material sourcing to final delivery, run smoother and faster. The aim is to remove the friction that slows your team down and eats into margins.
For many manufacturers, the current setup leaves little room to adapt:
- Machines follow fixed schedules, even if demand drops or spikes
- Downtime is addressed after it happens, causing unnecessary delays
- Data is scattered across systems, is hard to access, and rarely updated in real time
- Planning happens in spreadsheets that don’t reflect what’s actually happening on the floor
These gaps cause missed delivery windows, overproduction, idle time, and rising operational costs. Even worse, they make it hard to respond when something goes wrong. Unplanned downtime alone costs manufacturers $50 billion per year.
This is where AI changes the game. AI brings visibility and real-time decision-making to the forefront, enabling manufacturers to identify problems early and adapt quickly.
Improving data flow and decision-making is just part of the solution. To fully unlock efficiency, AI also optimizes your production layout, ensuring it supports the speed and flexibility today’s operations require.
How AI Optimizes Production Line Layout
In addition to improving data flow and decision-making, AI can optimize the physical layout of your production line.
A poorly designed layout leads to:
- Longer routes for workers, slowing down operations
- Materials getting stuck in the wrong places
- Idle machines, waiting instead of running
- Errors creep in as pressure builds in the wrong places
A well-optimized layout fixes this. It cuts down unnecessary movement, improves flow, and keeps every step of the process tightly linked. You get more done, with less effort, and fewer mistakes.
AI makes this even smarter.
It suggests changes, runs simulations, and tests possibilities. It uses your data to find the layout that actually works, not just the one that looks good on paper.
You can:
- Spot bottlenecks before they disrupt flow
- Balance workloads across the floor
- Improve line efficiency without constant trial and error
For example, a meat processing plant used AI to optimize its workstation layout with the 5S methodology.
The results?
- 30% drop in changeover times
- Fewer workplace accidents
- Smoother, safer, faster operations
Most layouts weren’t built for today’s pace. Let’s take a closer look at where they fall short and why even small inefficiencies can turn into big setbacks.
5 Challenges in traditional production line layout
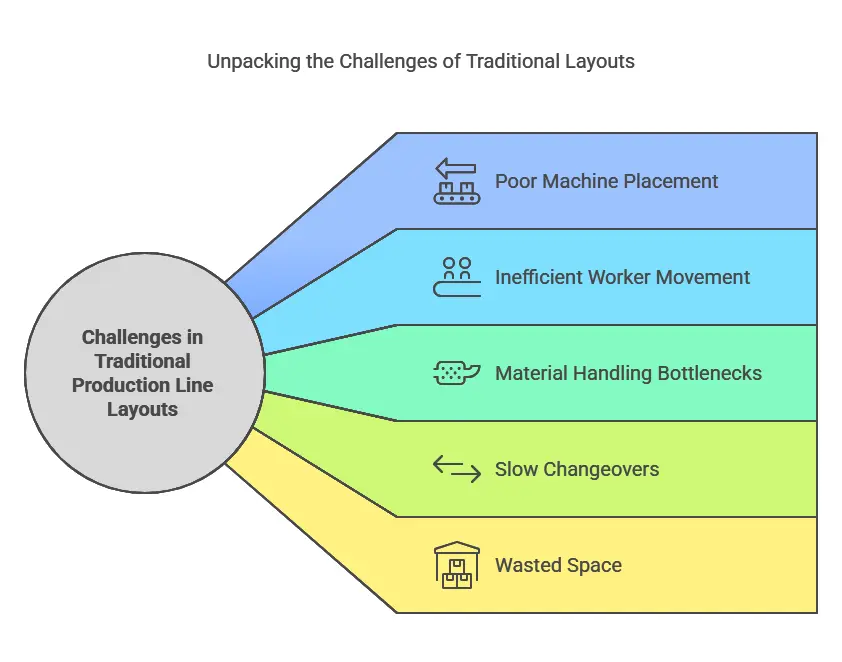
Most production line layouts were designed in a different era, when demand was steady, product lines were limited, and changes were rare.
Modern manufacturing is fast, complex, and constantly shifting. Product variety is higher. Timelines are tighter. Customers expect more, and they expect it yesterday.
Here’s what slows things down:
#1 Poor machine placement
When machines are placed for short-term ease rather than workflow efficiency, it creates costly bottlenecks. Common mistakes include:
- Grouping equipment by type rather than production sequence
- Prioritizing installation convenience over operator movement
- Ignoring material flow paths
Many US car manufacturers once grouped machines by function. Stamping presses were in one area, while welding stations were in another. As a result, car parts had to be moved across the factory multiple times. This caused delays and increased expenses.
#2 Inefficient worker movement
When workstations, tools, or materials are poorly arranged, operators waste significant time:
- Walking unnecessarily between stations
- Searching for parts/tools
- Waiting due to unbalanced workflows
Boeing realized this and worked on cutting worker movement inefficiencies by redesigning assembly lines by using digital tool tracking. The company was able to cut production time by 24%.
#3 Material handling bottlenecks
Inefficient material handling leads to delays when materials are stored far from where they are needed or pile up in the wrong locations. Poor warehouse organization, unpredictable supply deliveries, and unoptimized transport routes can create bottlenecks, slowing down production and increasing costs.
Ford tackled material handling bottlenecks by optimizing storage and automating transport. At Kansas City Assembly Plant, AI-driven simulations improved labor planning, cutting aisle congestion and delays.
#4 Slow changeovers
Long changeover times are a major cause of inefficiency, especially when production lines need to switch between different products.
#5 Wasted space
Facility space is either:
- Overcrowded, leading to cluttered aisles, safety hazards, and workflow bottlenecks
- Underutilized, causing increased overhead costs in empty zones
You’ve seen the problem. You’ve seen where traditional methods fall behind. Now let's see how AI helps you turn insight into action.
How can you use AI to optimize production lines and productivity?
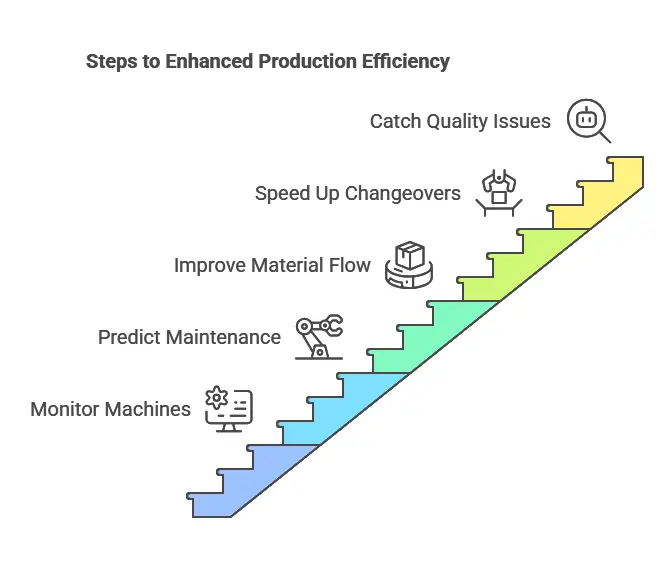
AI flips the script by turning reactive production into predictive production.
It helps you:
- Predict failures before they happen
- Adjust schedules on the fly
- Balance workloads across lines
- Maintain quality without slowing down
“We’re scaling artificial intelligence along the value chain—from development and production through to sales. In the foreseeable future, every process at the BMW Group will be AI-supported.”
~ Marco Görgmaier, Vice President Enterprise Platforms and Services, Data, Artificial Intelligence, BMW Group
Artificial Intelligence at BMW Group
And you don’t need to be BMW or Tesla to do it.
Mid-sized companies are already leveraging AI to reduce downtime, improve margins, and stay competitive in a challenging market. The key to these successes? Strong data analytics that surface the right insights at the right time.
AI’s power lies in its ability to optimize production in real-time—tracking machines, materials, schedules, and output. With AI in place, you can spot potential issues before they escalate, optimize your schedule on the fly, and ensure a smooth, continuous flow across shifts.
Of course, none of this is possible without a strong data foundation. AI is only as effective as the data it can access and act upon.
That’s why 5X offers an end-to-end data & AI platform that pulls in live data from every part of your production line—machines, schedules, and even operator input, ensuring you never have to work with disconnected tools or outdated information.
Here’s how artificial intelligence production actually works on the floor:
#1 Monitor machines in real time
Your maintenance teams rely on fixed schedules or respond to alerts when machines stop or slow down.
What AI enables: You install edge sensors (or integrate with existing PLCs), then feed that data—vibration, temperature, pressure—into an AI model trained to detect anomalies. If motor vibration increases by 5% beyond the baseline, the system alerts you before a failure occurs.
Where to start: Start with high-impact equipment like injection molding, CNC machines, or chillers. Feed real-time signals into a central dashboard.
#2 Predict maintenance needs
You plan maintenance in Excel, by calendar or shift hour count.
What AI enables: AI learns from past breakdowns, usage hours, and sensor data to predict when parts will fail or need service. It then recommends service before performance drops.
Where to start: Digitize your past service logs and connect them to live machine data. Train a model to flag patterns before breakdowns happen.
Take a page from General Electric (GE) that implemented AI-driven predictive maintenance, leading to significant improvements in efficiency, cost savings, and operational uptime.
#3 Improve material flow
You run daily schedules based on planner inputs, often without real-time machine feedback.
What AI enables: AI looks at demand, line capacity, workforce availability, and shift hours—and builds optimized schedules in minutes. If a line goes down or demand changes, it recalculates instantly.
Where to start: Use AI to run what-if simulations on one product line. Measure how much faster it adjusts to last-minute order changes or unplanned machine downtime.
For instance, ArcelorMittal uses AI models (inspired by ant colony behavior) to build minute-by-minute optimized production sequences. This dramatically improves flow and utilization.
#4 Speed up changeovers
You follow fixed changeover steps with limited visibility into where time is lost.
What AI enables: AI records every step during changeovers across multiple shifts. It analyzes patterns to show which steps take longest and suggests faster setups or operator instructions.
Where to start: Record 10 recent changeovers on your most flexible line. Let AI identify bottlenecks and opportunities for parallel steps or automation.
Cipla, a prominent pharmaceutical manufacturer, leveraged AI-powered smart scheduling to achieve a significant reduction of 22% in changeover times. By implementing AI-driven solutions, Cipla optimized production sequences and minimized downtime, leading to faster production cycles without compromising product quality or safety.
#5 Catch quality issues early
You inspect products at end-of-line. If defects are caught, you rework. If not, you ship poor quality.
What AI enables: AI-powered vision systems inspect components in real time. It flags defects—scratches, dents, misalignments—instantly. Models learn over time and get better at spotting anomalies, broadening your business intelligence ecosystem
Where to start: Install vision systems at one inspection point. Train a model on what good vs. defective looks like. Use this as a pilot before rolling it out plant-wide.
Coca-Cola is already doing this. They employ AI-powered visual inspection systems to identify defects in thousands of units per minute, ensuring high product quality while cutting manual work.
AI-Powered Production Line Optimization
You’ve already tackled the basics, streamlined workflows, reworked layouts, and fixed the obvious inefficiencies. But traditional tools can only take you so far.
Real transformation begins when your systems can think, learn, and adapt in real time.
This is what AI-powered optimization can do. It helps you predict downtime, improve layouts, and boost throughput, instantly.
To make AI truly effective, you need a connected data foundation that pulls in live information from across your operations. This is where 5X comes in.
5X gives you a clean, connected data platform that turns raw factory data into ready-to-use insights for AI models.
This helps you start predicting downtime, optimizing layouts, and improving throughput with models that actually work.
How is AI used to reduce defects in manufacturing?
How to reduce defects in manufacturing?
Building a data platform doesn’t have to be hectic. Spending over four months and 20% dev time just to set up your data platform is ridiculous. Make 5X your data partner with faster setups, lower upfront costs, and 0% dev time. Let your data engineering team focus on actioning insights, not building infrastructure ;)
Book a free consultationHere are some next steps you can take:
- Want to see it in action? Request a free demo.
- Want more guidance on using Preset via 5X? Explore our Help Docs.
- Ready to consolidate your data pipeline? Chat with us now.
Table of Contents
Get notified when a new article is released
Get an end-to-end use case built in 48 hours
Get an end-to-end use case built in 48 hours
How retail leaders unlock hidden profits and 10% margins
Retailers are sitting on untapped profit opportunities—through pricing, inventory, and procurement. Find out how to uncover these hidden gains in our free webinar.
Save your spot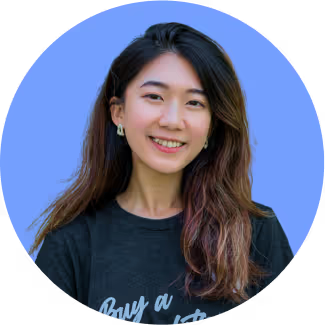
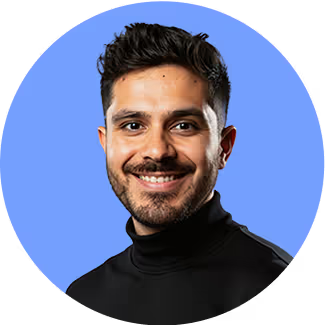