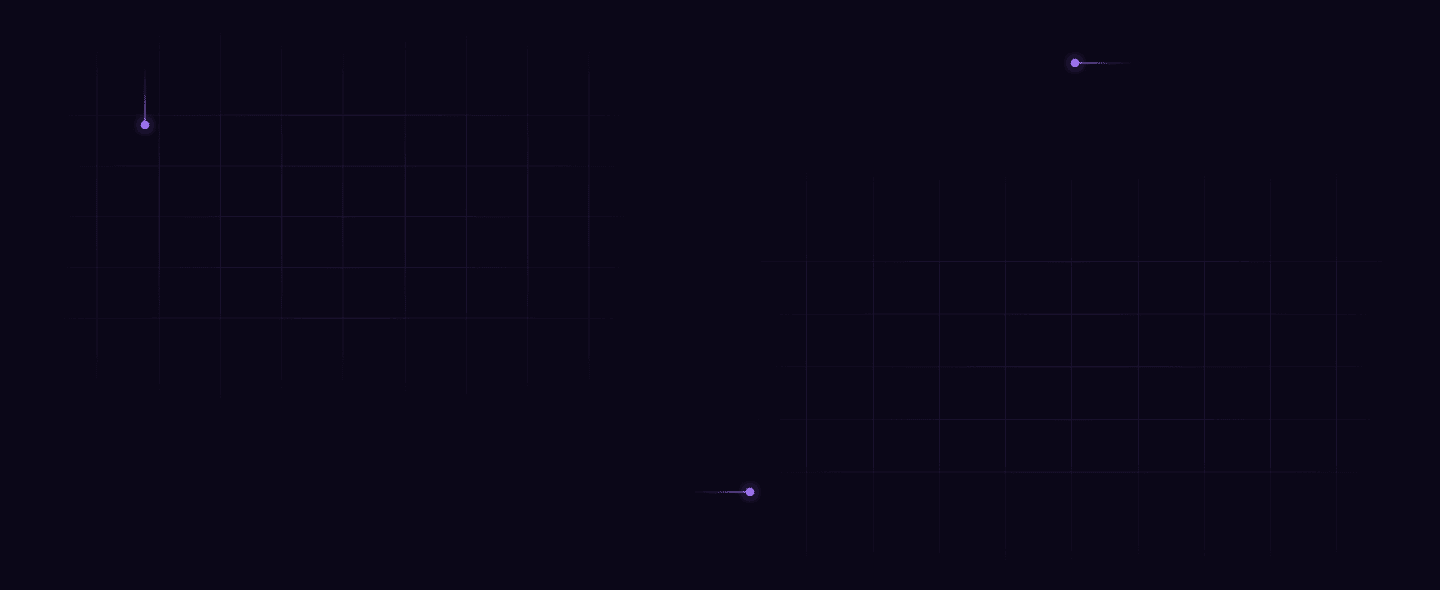
In the high-stakes world of manufacturing, even the smallest defect can escalate into significant financial drain. It’s a glaring issue, especially considering the $8 trillion lost annually to inefficiencies and defects across the industry. For companies still on the cusp of digital transformation, the pressure is mounting.
“Companies that use this opportunity to create the foundations for the large-scale application of AI in manufacturing will get ahead of the competition and maintain their advantage by accelerating their AI journey.”
~ Christian Michalak, Executive Vice President at Capgemini Invent
Artificial Intelligence (AI) enters this scenario not just as an innovative tool but as a transformative force. This tech isn't about replacing the human element; it’s about supercharging it. In fact, one car manufacturer used AI to detect defects with 97% accuracy. This…is a revolution, transforming your manufacturing from reactive to proactive, all without adding a single extra hour or body on the shop floor.
So, let’s find out how manufacturers are reducing manufacturing defects by using AI and how you can do it too!
5 Benefits of implementing AI in manufacturing
.webp)
The manufacturing sector is tapping into AI to streamline operations and boost efficiency. Here’s a look at how AI is making a real difference:
#1 Enhanced quality control
AI tools scrutinize every part of the production line in real time. They catch defects and inconsistencies that might slip past human inspectors, leading to higher quality products and increased customer satisfaction.
#2 Predictive maintenance
AI can forecast equipment failures before they disrupt production. This predictive capability allows for timely maintenance, reducing downtime and saving on repair costs. Studies indicate that implementing AI for predictive maintenance can decrease unplanned outages and extend the lifespan of machinery.
Also read: Predictive Sales Analysis: The Future of Sales Forecasting
#3 Optimized production processes
AI analyzes operational data to fine-tune manufacturing processes, enhancing efficiency and reducing waste. This means lower production costs and less material waste.
Some manufacturers have seen their efficiency rates jump significantly after integrating AI systems into their workflows.
#4 Supply chain optimization
AI predicts demand trends and optimizes inventory levels, helping to streamline supply chains. This results in faster delivery times and reduced holding costs. AI-driven analytics help identify the most efficient supply routes and the best possible suppliers.
#5 Worker safety and ergonomics
AI monitors and analyzes workplace conditions to predict and mitigate potential safety hazards. This proactive approach not only reduces the risk of accidents but also boosts overall worker productivity by ensuring a safer and more comfortable working environment.
Also read: Running a cost-effective business by reducing manufacturing costs using AI
4 manufacturers betting big on reducing manufacturing defects with AI
In the high-stakes world of manufacturing, even a tiny defect can mean substantial financial losses—a ripple effect that no company wants to face. Yet, the advent of AI-driven zero-defect manufacturing is poised to make such imperfections as obsolete as floppy disks. Here's how pioneering companies are harnessing AI to revolutionize their manufacturing processes and drastically reduce defects:
#1 General Motors
General Motors employs AI to analyze images from cameras mounted on assembly robots. This technology helps spot signs of potential failure in robotic components. In a pilot test involving 7,000 robots, it successfully detected 72 instances of component failure, preventing unplanned outages and substantial financial loss. Given that production-line downtime can cost up to $20,000 per minute, the savings are immense.
#2 Volvo
Volvo utilizes its large-scale dataset Early Warning System to analyze over one million events each week. By monitoring variables like temperature increases or abnormal pressure readings, the system assesses their impact on breakdowns and product defects, thus enhancing overall product reliability.
#3 Audi
At its Ingolstadt press shop, Audi has implemented an AI-based image recognition system. Cameras installed in the presses capture images of pressed sheet metal, which are analyzed to identify even the smallest cracks. Trained with several million test images from Audi’s and other Volkswagen plants, this system achieves high accuracy in quality inspections.
#4 Fiat Chrysler China
Chrysler China uses computer vision to inspect the quality of powertrain assemblies. Their AI system is trained to detect improper assemblies or missing components like small screws, which are difficult for human eyes to discern. Defective parts are swiftly removed to a separate rework area, preventing quality issues for end-customers and avoiding costly production delays.
“The system is extremely fast and efficient, allowing defective parts to be taken off the main conveyor on a separate line to the rework area where they can be corrected. The process not only saves a lot of quality issues at the end-customer but also loss of valuable production time.”
~ Neeraj Tiwari, ex-Director manufacturing JV organization at Fiat Chrysler China
Credits: This information is based on insights from the Capgemini Research Institute: Scaling AI in Manufacturing Operations: A Practitioners’ Perspective.
5 Steps to start using AI to reduce manufacturing defects
“Data products are a great way to get answers to the question that data needs to be processed, to structure the flow of data and facilitate reuse across AI development projects.”
~ Felix Balhorn, Director, Intelligent Industry Data and Analytics, Capgemini Invent
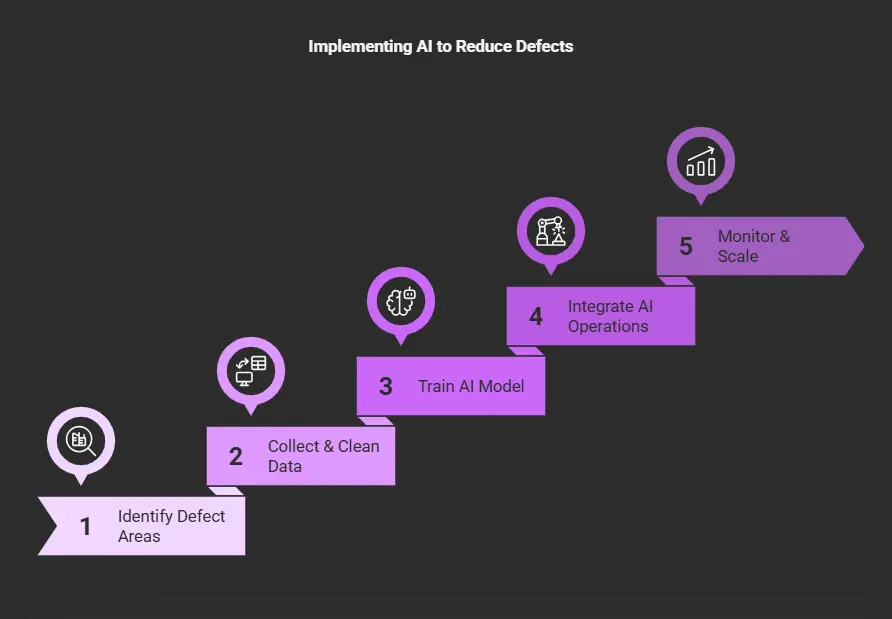
Using AI to reduce manufacturing defects doesn't have to be a head-scratcher. Here’s a streamlined, five-step guide for those ready to leverage AI, without getting bogged down by the technical mire. And for the heavy lifting, well, let’s just say we have a solution!
Step 1: Pinpoint the problem areas
First things first, scope out your production line to spot frequent defect zones—think assembly, painting, or welding.
For instance, in automotive manufacturing, paint imperfections often lead the defect parade.
Step 2: Gather and groom your data
AI is only as good as the data it consumes. Start harvesting data from the usual suspects—sensors, cameras, and machines. Focus on collecting everything from visual inspection feeds to operational logs.
“In data terms we have been organized around functional lines: development, production, procurement and so on, all historically kept their own data to themselves. Now we are integrating this into a big data lake that will involve the whole organization. In the next five to ten years we will have the potential to use machine learning to optimize the quality of our processes or we can get more efficient. And that means data becomes the gold nuggets of the future, helping us to optimize our products, get better customer views, and optimize our business models.”
~ Klaus Slaub, former CIO, BMW
So maybe start with equipping paint shops with high-resolution cameras to continuously monitor vehicle finishes.
Step 3: Train your AI
Use machine learning to educate your AI on what good and bad look like. This could involve training models with images of perfect and flawed finishes or using analytics to spot outliers in machine performance.
Example: An AI model learns the ropes by analyzing thousands of vehicle finish images, identifying defects down to a microscopic level.
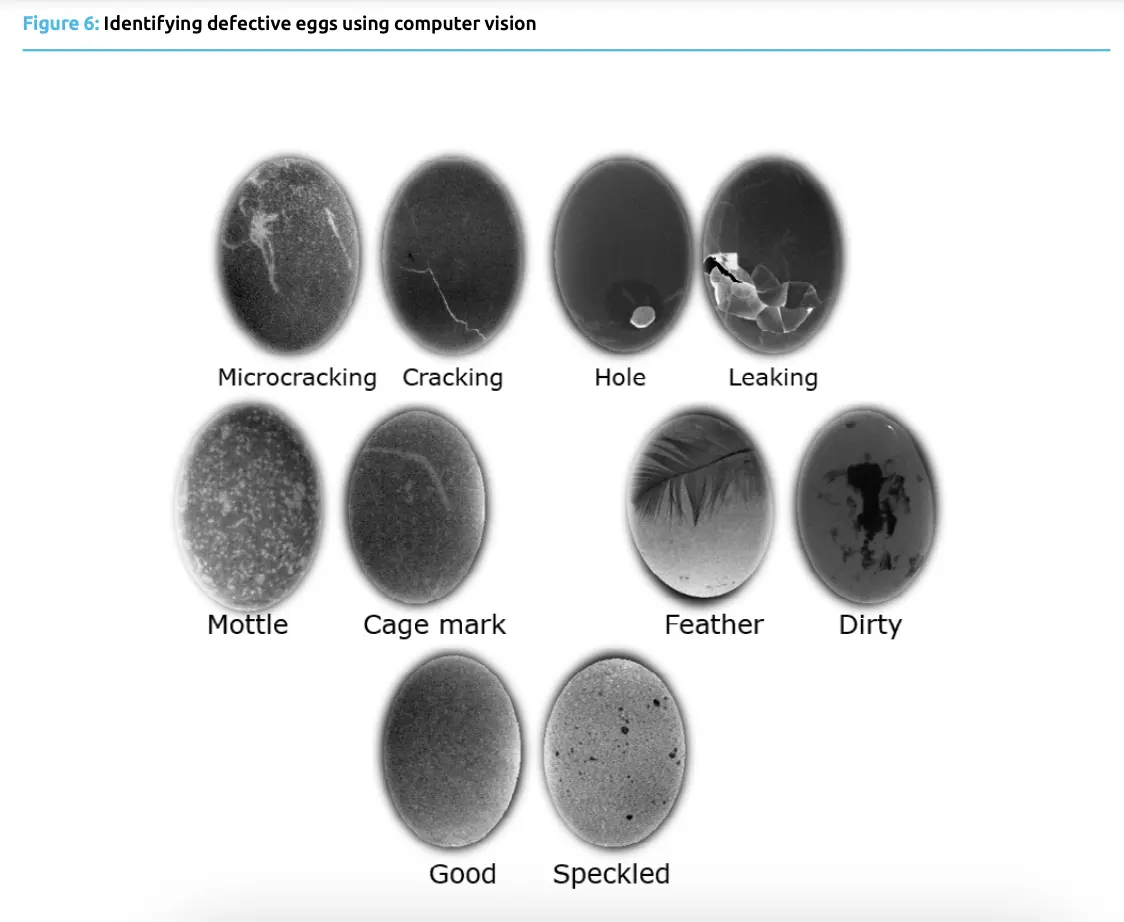
Source: Capgemini Research Institute Analysis
Step 4: Deploy AI on the front lines
With your AI trained, roll it out on the production floor. Set it up to alert staff instantly about potential defects or to tweak machine settings on the fly to avoid errors.
Example: As cars roll out of the paint booth, AI immediately flags any imperfections, allowing for quick fixes instead of costly reworks.
Step 5: Scale and optimize
Once you’ve nailed it in one area, take AI further. Monitor its impact, tweak as necessary, and then extend its reach to other stages like assembly or logistics.
Following a victory in paint defect reduction, the AI’s next mission could involve overseeing welding or assembly inspections.
How 5X helps you reduce manufacturing defects using AI
When it comes to reducing manufacturing defects, it’s not just about deploying technology; it’s about making your data work harder and smarter for you. Here’s how 5X transforms your approach to defect reduction through AI:
- Unified data integration: The platform brings together data from all your production stages and systems into one end-to-end platform. This holistic view enables you to analyze and pinpoint defect origins more accurately
- Predictive analytics: Apply predictive analytics to your historical and real-time data, forecasting potential defect trends. This insight allows you to make proactive adjustments to your production processes, significantly reducing the incidence of defects
- Quality control optimization: By leveraging the extensive data analysis capabilities of 5X, you can fine-tune your quality control measures. This ensures that your AI tools are precisely calibrated to detect and mitigate defects effectively at critical production stages
- Continuous learning and improvement: Our platform supports building AI models that learn continuously from new and existing data. This constant learning enhances the accuracy of your defect detection tools over time, adapting to changes in your manufacturing environment
- Scalability and flexibility: As your manufacturing demands grow, 5X effortlessly scales to manage increasing data volumes and complexity. Our platform's flexibility allows for the expansion of AI functionalities across various product lines and manufacturing sites
- Custom cloud deployment: Deploy 5X on your own cloud to maintain full control over your data security and compliance. The platform is designed to integrate seamlessly with your existing IT infrastructure, making it easy to manage and scale as needed
Embracing AI to reduce manufacturing defects
The shift towards integrating AI in manufacturing is not merely a trend, it's a revolutionary change that is dramatically reshaping the industry. As manufacturers adopt AI, they are discovering its broad-reaching benefits. AI not only enhances efficiency and quality control but also optimizes supply chains and revolutionizes predictive maintenance.
At 5X, we understand that the leap to AI-powered manufacturing might seem daunting. That's why we've designed our platform to seamlessly integrate with your existing systems, ensuring a smooth transition. Whether it's unifying your data, enhancing real-time monitoring, or scaling AI applications across your production lines, 5X makes the process intuitive and effective.
How is AI used to reduce defects in manufacturing?
How to reduce defects in manufacturing?
How can AI be used as part of defect inspections?
Building a data platform doesn’t have to be hectic. Spending over four months and 20% dev time just to set up your data platform is ridiculous. Make 5X your data partner with faster setups, lower upfront costs, and 0% dev time. Let your data engineering team focus on actioning insights, not building infrastructure ;)
Book a free consultationHere are some next steps you can take:
- Want to see it in action? Request a free demo.
- Want more guidance on using Preset via 5X? Explore our Help Docs.
- Ready to consolidate your data pipeline? Chat with us now.
Table of Contents
Get notified when a new article is released
Get an end-to-end use case built in 48 hours
Get an end-to-end use case built in 48 hours
How retail leaders unlock hidden profits and 10% margins
Retailers are sitting on untapped profit opportunities—through pricing, inventory, and procurement. Find out how to uncover these hidden gains in our free webinar.
Save your spot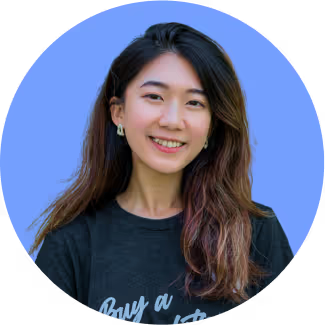
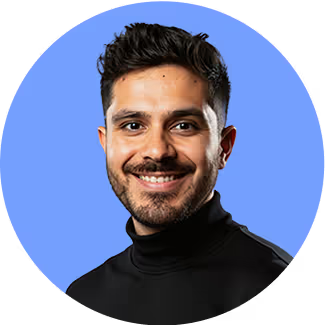